Bis ins kleinste Detail
Endlager Konrad
von Martin Kuhna Reportage
Beim Transport radioaktiver Abfälle darf auf den letzten Metern unter Tage nichts schiefgehen. Deshalb unterliegen auch die Fahrzeuge im Endlager rigorosen Qualitätskontrollen.
Zum Beispiel das Stapelfahrzeug. Es bringt die Abfallbehälter unter Tage in den Einlagerungskammern an ihren Platz. Das klingt nach einem schlichten Gefährt. Doch die Bundesgesellschaft für Endlagerung (BGE) hat einen Stapler der Superlative bestellt. „Im Grunde ist das Fahrzeug mehrfach überdimensioniert“, sagt Jens Kuschkowitz. Er ist bei der BGE Gruppenleiter der Endlagervorbereitung und zuständig für die Zentrale Planung und für Endlagerfahrzeuge. Überdimensioniert ist der Stapler aber nicht im Sinne von „schneller, höher, weiter“. Beim guten, alten Autoquartett wäre mit ihm also kaum zu punkten. Im Gegenteil: Viele der eingebauten Extras dienen dazu, den starken Koloss zu begrenzen und zu bremsen – aus Sicherheitsgründen.
Der Hintergrund: Weil der Stapler in den Einlagerungskammern eingesetzt wird, gehört er bei der BGE zum „Qualitätssicherungsbereich 3.2“, das ist die allerhöchste Stufe. Im BGE-Regelwerk steht trocken, warum: Stufe 3.2 gilt demnach für Komponenten, „deren Versagen unmittelbar zu Aktivitätsfreisetzungen aus Abfallgebinden führen würde“. Konkret: Würde das Gebinde mit Abfällen aus größerer Höhe vom Stapler fallen, könnte der Behälter beschädigt werden. Im ungünstigsten Fall könnte radioaktive Strahlung freigesetzt werden. Und obwohl selbst dann sichergestellt ist, dass es nicht zu katastrophalen Auswirkungen kommen kann, soll so etwas gar nicht erst passieren.
Deshalb gibt es präzise Vorgaben, was der Stapler können muss, sagt Jens Kuschkowitz. Während der Fahrt darf der Stapler den Container nicht höher als 50 Zentimeter heben. Die Hubhöhe muss dem Fahrenden jederzeit angezeigt werden.Außerdem darf der Stapler auf keinen Fall schneller fahren als 10 Kilometer pro Stunde.
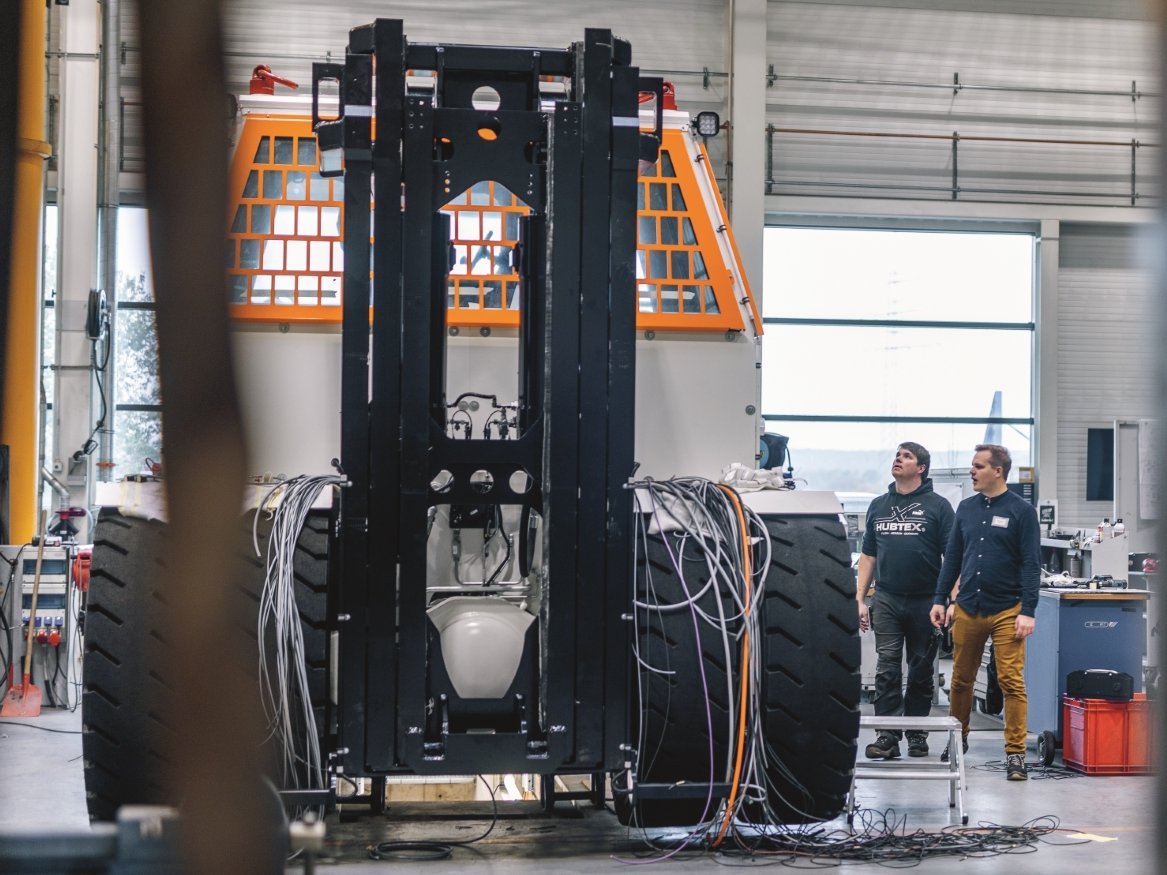
Höchstgeschwindigkeit: 10 Km/h
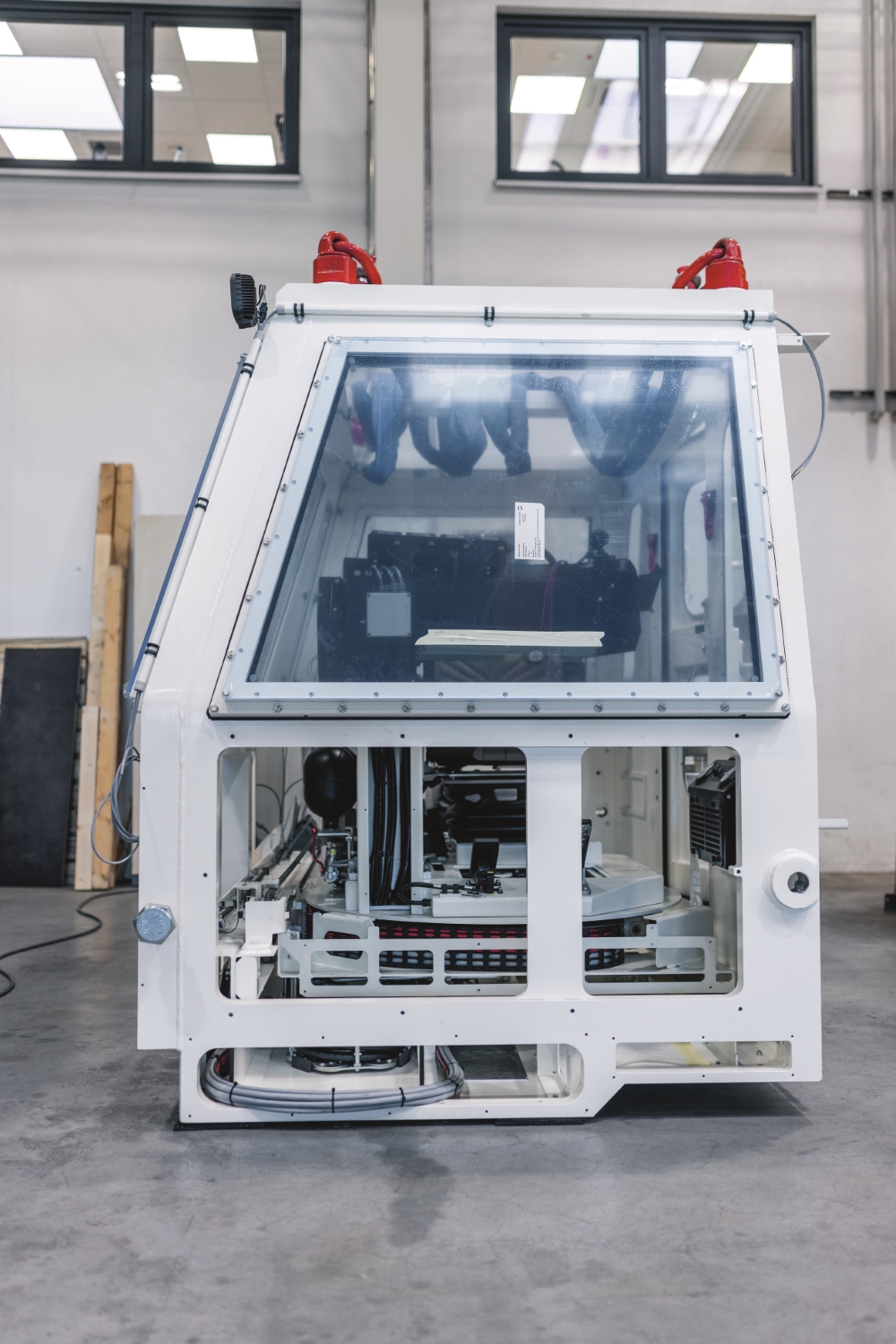
Das sind nur wenige Punkte von einer schier endlosen Liste detaillierter, von der Aufsichtsbehörde mehrfach überprüfter Vorschriften zu diesem Fahrzeug. Bei deren Einhaltung „haben wir keinen Spielraum“, sagt Kuschkowitz. Er wird diesen Schlüsselsatz wenige Minuten später noch einmal sagen. Denn darauf kommt es an: 50 Zentimeter maximale Hubhöhe und nicht mehr; 10 Kilometer pro Stunde Maximalgeschwindigkeit und nicht mehr – „auch nicht bergab oder mit Rückenwind“, wie Kuschkowitz sagt. Und das ist nur halb ein Scherz. Denn dass unerwartete Betriebszustände mitbedacht erden, ist wichtig.
Deshalb auch der überdicke Stahlrahmen und die Bleiverglasung der Führerkabine. Hier geht es um passive Sicherheit. Wie Kuschkowitz sagte: Das Fahrzeug ist überdimensioniert für die tägliche Routine. Aber nicht für den einen Fall, der aufgrund der unzähligen Sicherheitsbestimmungen – für diesen Stapler genauso wie für alle anderen Prozesse im Zuge der Endlagerung – extrem unwahrscheinlich ist.
Allein die Vorprüfunterlagen für die Fertigung dieses Stapelfahrzeuges umfassten mehr als 130 Aktenordner, sagt Stephan Bayer, Leiter der Stabsstelle Qualitätssicherung im Bereich Konrad. Natürlich gibt es solch ein Fahrzeug nicht von der Stange: Es musste von Grund auf neu entworfen werden. Nachdem der Hersteller Hubtex die Ausschreibung gewonnen hatte, war das Unternehmen durchgängig an Planung und Konstruktion beteiligt. Im Herstellerwerk, sagt Bayer, würden nun beim Bau der Stapler Tausende Seiten von Prüfplänen abgearbeitet. Das geht nur, weil im Fuldaer Werk eine komplementäre Qualitätssicherung existiert, die sich an den Standards des Auftraggebers orientiert und sie ergänzt. Überdies sind Vertreter*innen der BGE stets in Fulda präsent.
Eigentlich weckt das Wort Gabelstapler ja falsche Assoziationen. Die meisten denken dann wohl eher an die kleinen Fahrzeuge, die im Getränke- oder Baumarkt herumflitzen. In Fulda hingegen betreiben sie Sondermaschinenbau, darunter Flurförderfahrzeuge und Spezialstapler für die Industrie. Was die Dimensionen betrifft, „fangen wir da an, wo andere aufhören“, sagt Frank Knurr. Er ist bei Hubtex Projektleiter für die BGE-Fahrzeuge.
Was da für andere Kunden abholbereit in der Halle steht, sieht tatsächlich beeindruckend aus, nach „Heavy Duty“. Jede Maschine wird für jeden Kunden speziell entworfen und gebaut – „zwei gleiche Fahrzeuge sind bei uns schon eine Serie“.
„Zwei gleiche Fahrzeuge sind bei uns schon eine Serie“ Frank Knurr
Stapler mit 50 Tonnen Eigengewicht
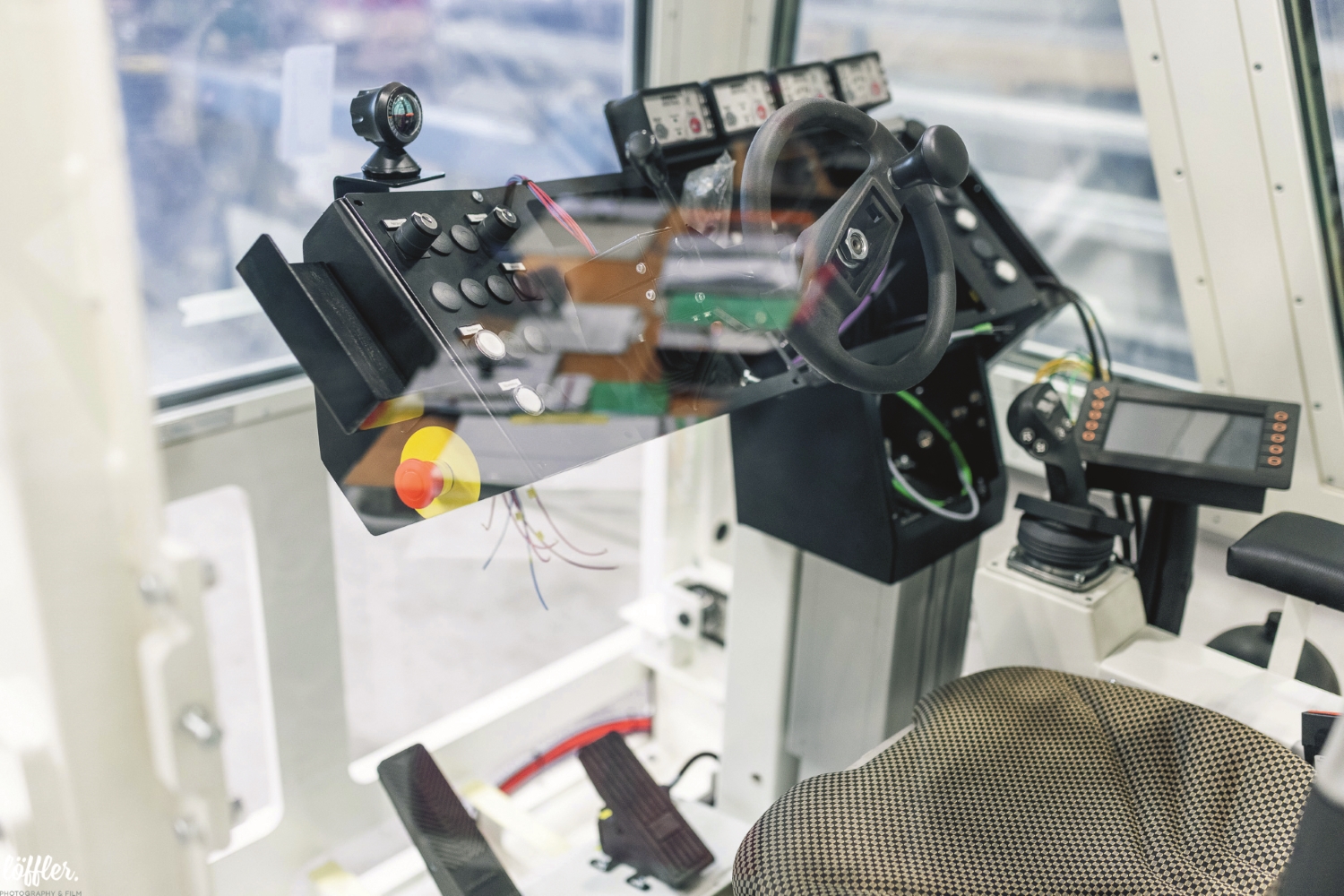
Die BGE sei für Hubtex eine normale Kundin, sagen sie in Fulda betont gelassen. Und fügen dann augenzwinkernd hinzu: „Die Anforderungen sind aber schon speziell.“ Ein Stapler mit 50 Tonnen Eigengewicht, das ist auch bei Hubtex am oberen Ende der Skala. Ein kurvengängiges Fahrgestell mit Knickgelenk, ähnlich wie bei den Gelenkbussen, wird auch nicht alle Tage gewünscht. Speziell ist aber vor allem, dass die BGE bei Hubtex ein eigenes Büro eingerichtet hat. Und während andere Kunden in der Regel am Anfang und in der Schlussphase eines Projektes das Werk besuchen, ist von der BGE immer jemand da, jede Woche.
Es gibt zwei Arbeitsvorbereiter nur für das BGE-Projekt. Für sie hat die BGE eigens eine kleine Zweitwohnung in der Stadt angemietet. Im eigenen Projektbüro stehen große Schränke voller orangefarbener Aktenordner. „Bei der BGE kommt in Sachen Dokumentation wirklich noch mal ne Schippe drauf im Vergleich zu anderen Kunden“, sagt Christopher Erb, bei Hubtex für die Qualitätssicherung verantwortlich.
Für jedes einzelne Teil des Staplers enthalten die zahllosen BGE-Ordner Fertigungsaufträge. Mit detaillierten Vorschriften, etwa zum Rohmaterial. „Wir stellen sicher, dass kein Material verwendet wird, das nicht verwendet werden darf.“ Falls die Lieferfirma keine im Sinne der BGE vollständige Dokumentation der Materialeigenschaften beibringt, muss Hubtex eigene Prüfungen vornehmen oder in Auftrag geben.
Und so wird jede einzelne Stahlplatte entsprechend ihren Eigenschaften gekennzeichnet. Bei der Bearbeitung testiert der Mann an der Maschine jeden Schritt; ebenso der hoch qualifizierte Schweißer, wenn er Bauteile sorgfältig zusammengefügt hat. Und am Ende wird jedes fertige Teil noch einmal überprüft, von sechs Augen: durch AG, AN und SB.
AN steht in den Protokollen für die Vertreter*innen des Auftragnehmers, AG für die des Auftraggebers und SB für die Sachverständigen der Behörde. Christopher Erb demonstriert das Verfahren an einem unscheinbaren Kleinteil: einer verstellbaren Spannwegverlängerung. Zunächst wird das Teil auf einem Arbeitstisch mit einem Präzisionsmessgerät auf korrekte Maße geprüft. Erst von Erb selbst (AN), die BGE vor Ort ist (AG), schließlich vom Vertreter des TÜV (SB). Danach wird mithilfe einer Farbeindringprüfung nach mikroskopisch kleinen Rissen im Material gesucht.
Das kleine Werkstück wird mit einer lilafarbenen Flüssigkeit namens Penetrant eingeschmiert. Nach der vorgeschriebenen Trockenzeit wird die Farbe abgewischt und das Werkstück mit einem kalkartig weißen Entwickler bestrichen. Gäbe es winzige Risse im Material, dann würde die grell-lila Farbe nun aus dem Stahl herausgesogen und im Entwickler sichtbar. Doch alles bleibt weiß. Keine Risse. Die Prüfer ziehen jeder einen kleinen Taschenstempel hervor, drücken ihn auf die vorgesehene Stelle im Prüfbericht und fügen ihr Kürzel hinzu.
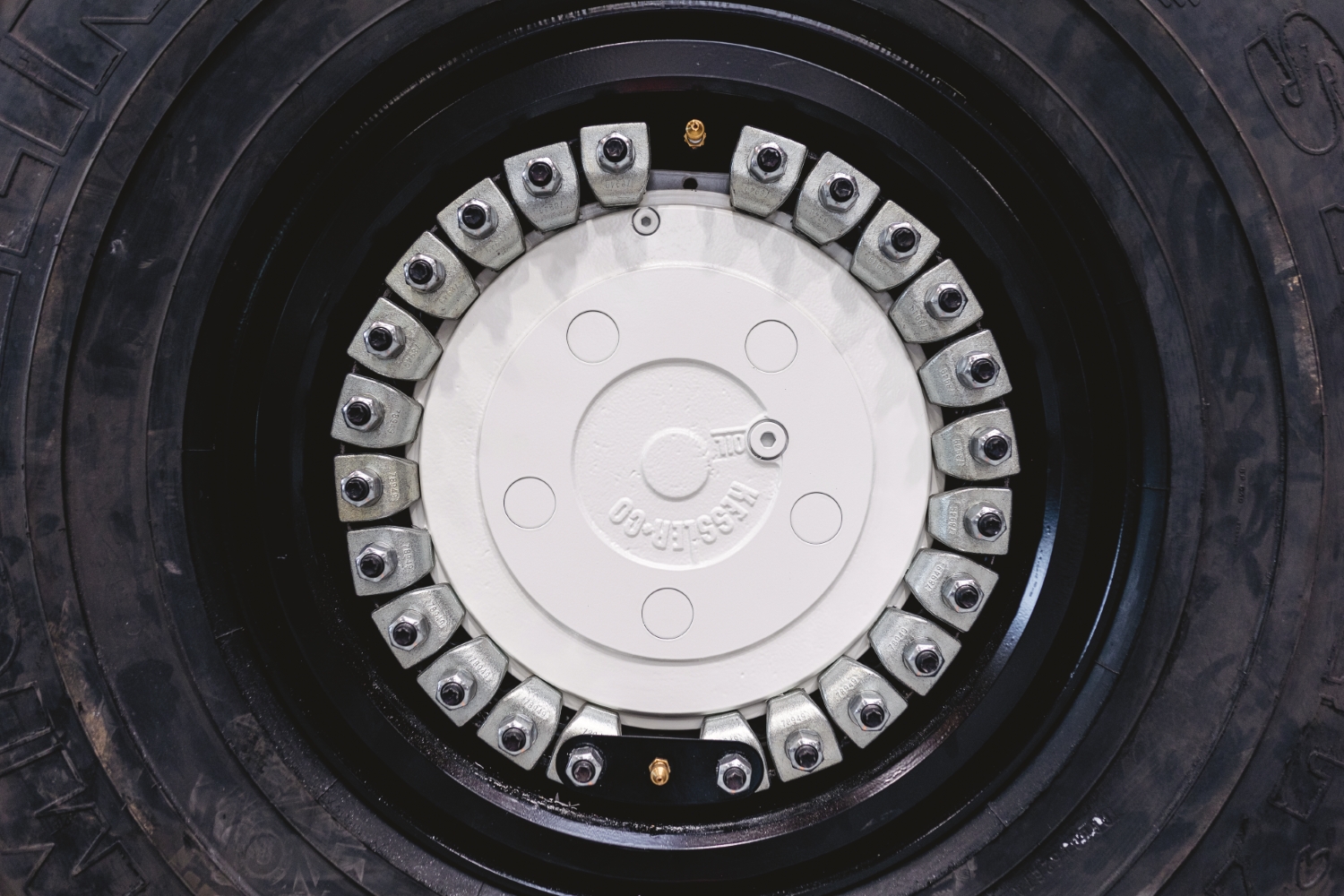
Jede Schweißnaht wird geprüft
Bei diesem Kleinteil ist der Test rasch abgeschlossen. Bei großen Teilen, sagt Erb, dauere dieser Test schon mal vier Stunden. Und neben der Farbeindringprüfung gibt es noch andere: die Ultraschallprüfung oder die Magnetpulverprüfung. Zuvor, bei der Werkstoffprüfung, Dinge wie Zugversuch, Kerbschlagbiegeversuch oder Warmkontrolle. Ein ähnliches Bild bei Schweißungen: An manchen Stellen ist genau vorgeschrieben, wie etwas geschweißt wird – mit welchem Schweißgerät etwa und mit welcher Stromstärke. Und auch jede Schweißnaht wird dann geprüft.
„Ein Riesenaufwand“, sagt der Hubtex-Mitarbeiter Ralf Laubach, der gerade an einem anderen Fahrzeug für die BGE schweißt, dem Seitenstapelfahrzeug. Aber dass seine Arbeit so minutiös überprüft wird, nimmt Laubach gelassen. Er hat 30 Jahre Erfahrung – und geprüft ist er selbst auch, klar, gemäß BGE-Vorschrift: „Der H (Hersteller) muss den Großen Eignungsnachweis nach DIN 18800 Teil 7 besitzen.“
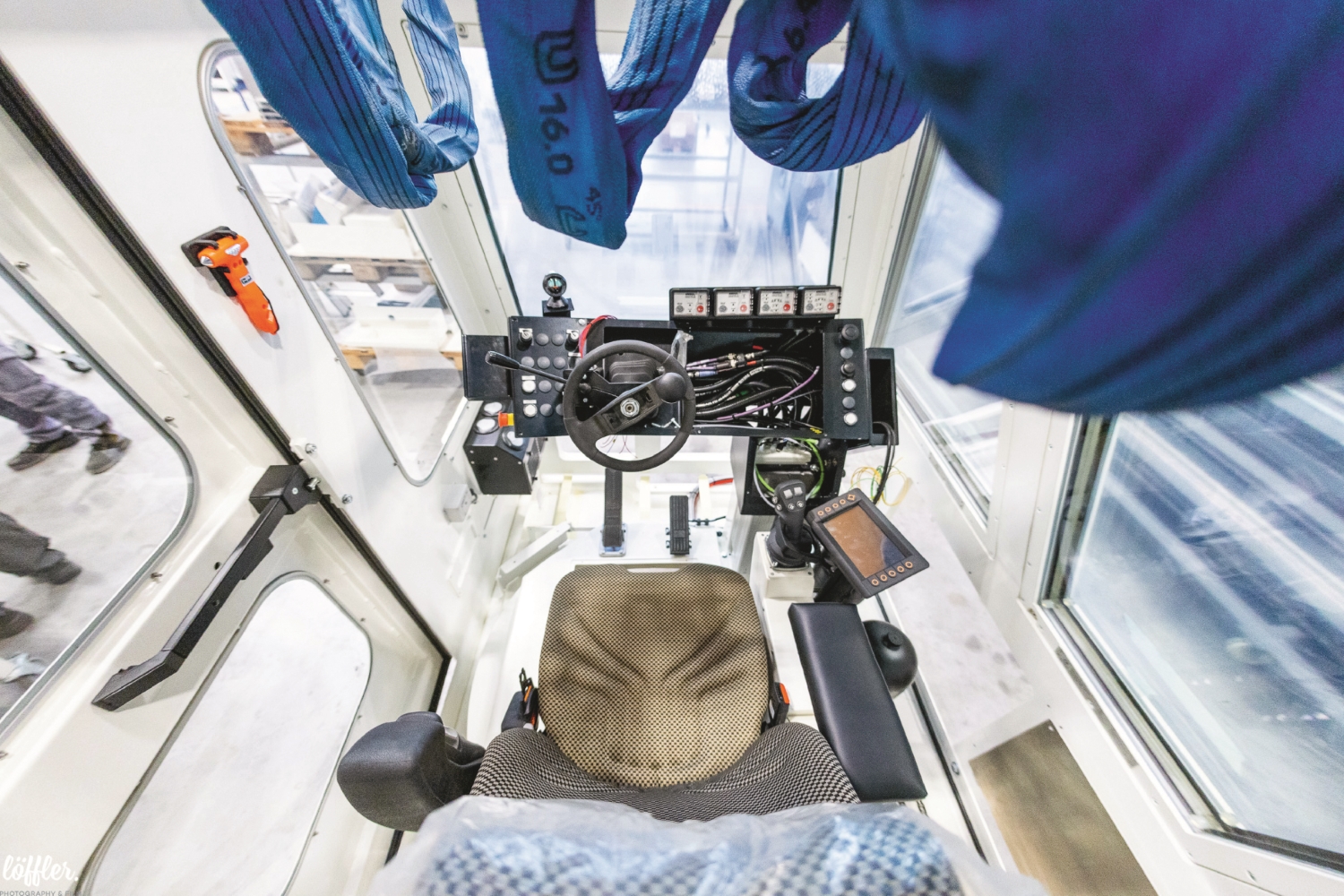
Während Laubach am Rahmen des Seitenstaplers schweißt, ist wenige Meter entfernt der Hubstapler für die Endlagerkammern gerade fertig montiert worden. Bei Hubtex nennen sie das einen Schwarzaufbau, und deshalb wird der Riese auch gleich wieder zerlegt. Mit illegaler Beschäftigung hat das nichts zu tun, es handelt sich vielmehr um einen Testaufbau. Schwarz bezieht sich darauf, dass die Einzelteile unlackiert zum Stapelfahrzeug zusammengesetzt wurden – zur Probe. Nach der Demontage werden die Teile lackiert, weiß und schwarz. Dann werden sie wieder zusammengesetzt.
Und dann geht es weiter mit den Tests und Prüfungen, bis zur Abnahme des fertigen Produktes. „Für die Tests werden auf dem Werksgelände die untertägigen Einlagerungskammern von Schacht Konrad nachgebaut“, sagt Projektleiter Knurr. „Und in einem benachbarten Steinbruchkönnen wir Strecken anlegen mit genau definierten Gefällewerten.“ Dann wird sich zeigen, ob der neue Hubstapler auch bergab wirklich nur 10 Kilometer pro Stunde läuft und kein bisschen schneller. Auch mit Rückenwind nicht.
Ein immenser Aufwand
Wer gern über Vorschriften lästert und über Bürokratie seufzt, wer auf das Prinzip „Schaun wir mal“ und „Passt schon“ setzt, für den wäre der Bau dieses Stapelfahrzeuges ein Alptraum. Auch verbissene Kostensenker müssten leidensfähig sein, denn: „Das ist schon ein immenser Aufwand, auch personell“, sagt Knurr. „Gut so“, denkt man als durchschnittlich-chaotischer Mensch beim Blick auf dicke Stahlteile, solide Schweißnähte und endlos gereihte Aktenordner – zumal wenn der gesuchte Prüfbericht mit einem Griff gefunden wird. In Klarsichthülle. Und zusätzlich digital gesichert, versteht sich.
Wer gern über Vorschriften lästert, für den wäre der Bau dieses Hubstaplers ein Alptraum
Die HUBTEX GmbH & Co. KG in Fulda wurde 1981 gegründet. Sie stellte zunächst Spezialfahrzeuge für die Textilindustrie her, daher das „tex“ im Namen. Heute produziert HUBTEX mit rund 500 Mitarbeiter*innen am Standort Fulda Flurförderzeuge, Seiten-, Hub- und Mehrwegstapler für lange, schwere, sperrige und empfindliche Güter in verschiedenen Industriezweigen.